
Mooring bollard is a vital component of any mooring system. It is usually the short post and is used as the anchor point for mooring lines to be fixed to secure the vessel alongside jetties/quay, berths, wharves and dolphins in ports and harbors.
Since the beginning of maritime history, people have been using wooden posts or iron structures for this purpose. With the advancement of manufacturing technology, engineers and manufacturers of today have considered the strength and durability of materials while also providing a safety factor as a safety cushion.
Mooring bollard is a simple and essential mooring device. However, not all bollards are created equal. Different design profiles, sizes and mooring line capacities are considered to adjust in each port. The suited mooring system applications considers the physical conditions, and the type of ships it will serve.



Designing and choosing the right components are a big part in marine construction. It is crucial to know what type of material to be utilized. Ductile cast iron, cast steel and stainless steel are some of the main materials used to make marine mooring bollards. They each have advantages in their applications.
In this article, we will focus mainly on the difference of cast iron vs cast steel.
Carbon content is the main difference
Iron and steel are both ferrous metals composed primarily of iron atoms. Pure elemental iron is too soft to be useful but when mixed with carbon, it gets harder, and therefore more useful. In fact, the carbon composition is the main distinction between cast iron and steel. Cast iron typically contains more than 2 percent carbon, while cast steel often contains between 0.1–0.5 percent carbon.
Impact resistance
Steel is excellent at withstanding sudden impacts without bending, deforming, or breaking due to its ability to withstand high stress and strain forces.
Strength without ductility results in a brittle material that is highly susceptible to fracture—and cast iron is one good example of strength without ductility. Because of its brittleness, cast iron has a limited range of application.
While iron may be easier to work with in most casting applications, steel has an optimal mix of both strength and ductility for many applications, and it is extremely tough. Steel is the most widely used metal in the world due to its impact-resistant qualities and all-around load-bearing nature making it desirable for many mechanical and structural applications.

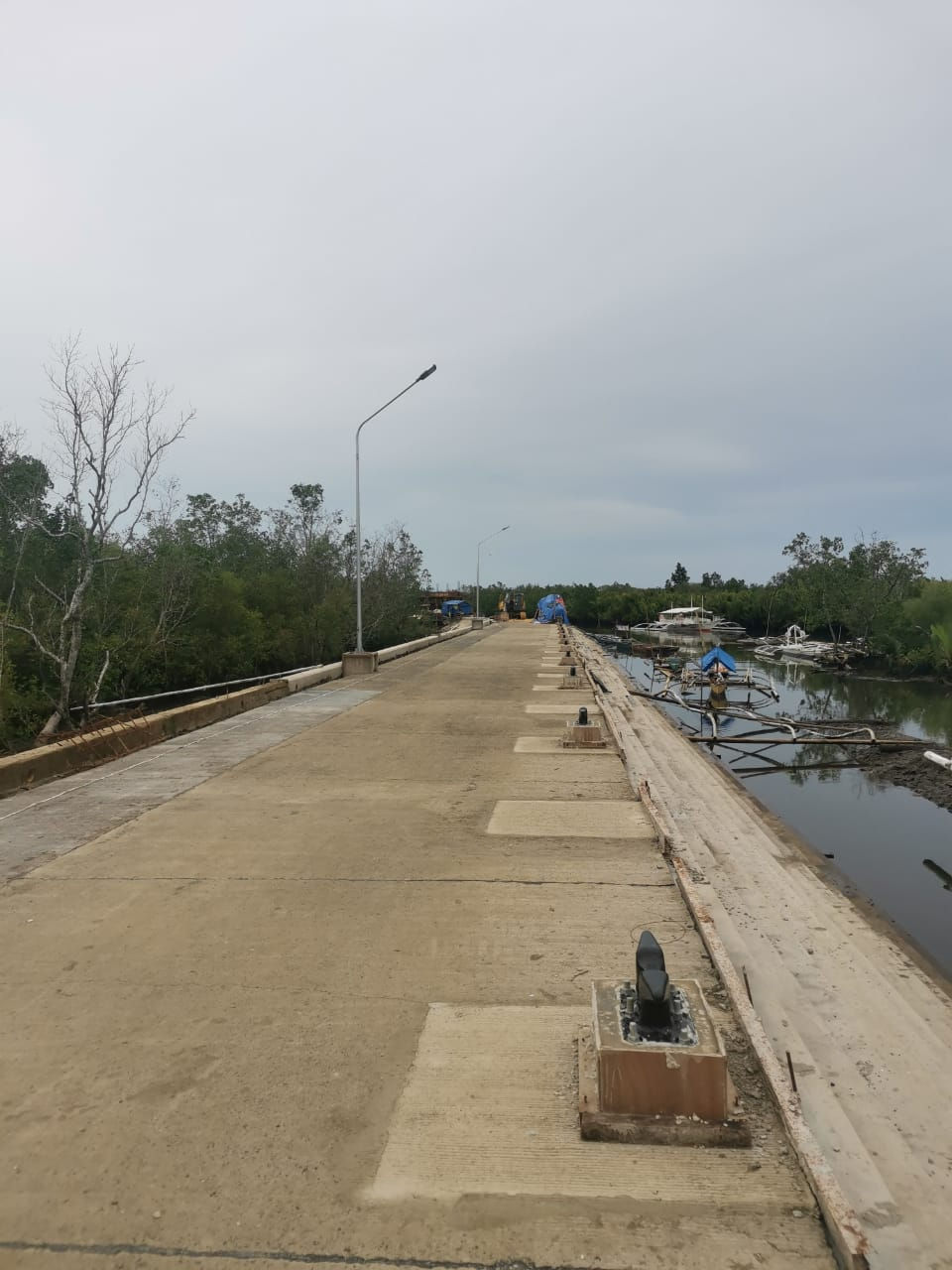
Corrosion Resistance
Iron has better corrosion resistance than steel. Both metals oxidize in the presence of moisture, but iron develops a patina to prevent deep corrosion of the metal's integrity.
The mooring bollards have long been exposed to a highly corrosive marine environment, which is easy to rust, so the mooring bollards require a durable coating system. Due to the wear and abrasion from the ropes, the mooring bollards need to be regularly maintained. The steel mooring bollards need to be painted often to maintain all intensity because it is more susceptible to the cast iron mooring bollards.
Wear Resistance
Cast iron has better resistance to mechanical wear than steel, specifically in friction-wearing situations.
Steel wears more readily than iron but may still be resistant to certain types of abrasion. This can be resolved by adding certain alloys that can help improve its abrasion qualities.
Cost
Cast iron is cheaper than cast steel due to its lower material costs, energy, and labor required to produce the final product. Raw steel is costlier to purchase, and it requires more time and attention to cast.
Alloys can be added to both iron and steel to engineer desired properties. For example, Manganese increases toughness, while chromium improves corrosion resistance and may also affect the cost of the material.

To summarize :
Materials | Advantages | Disadvantages |
Ductile Cast Iron | - Long service life
- High strength
- Good impact resistance
- High corrosion resistance
| The most expensive among the 3 types of materials. |
Grey Cast Iron | - Low cost per weight - Excellent corrosion resistance | - Low strength
- Low impact resistance
|
Cast Steel | - High strength - High impact resistance - Good cost per weight | Needs regular maintenance to prevent corrosion. |
Mooring bollards play an important role in ship mooring and the choice of the right material will greatly affect the operation of the marine facility. Ultimately, the right selection should also consider the factors such as the most demanding load combination possible, the type of marine structure and the adhesion of the surface into account. This will determine the most suitable shape, size and material of the bollard to ensure maximum quality and strength.


If you're looking for an industry leader in the production of bollards, then contact ESC Marine Systems.